Following our previous discussion on LED inspection, this article focuses on a compelling case study where IZAK Scientific developed a cutting-edge LED and shape inspection system tailored for high-volume production environments. This system exemplifies our commitment to innovation, quality, and efficiency, and demonstrates how our solutions can meet the rigorous demands of quality assurance, engineering, and production managers.
Project Overview
Mobileye, a leader in advanced driver-assistance systems, required an inspection system for their bare LED chips. The system needed to ensure homogeneous illumination and precise shape conformity, while operating seamlessly in a mass production setting. Key requirements included:
High-Speed Testing: The system must perform inspections in a few tens of seconds per batch of four units.
Durability: Components, particularly connectors, should withstand over 1 million fast insertions and removals.
Robustness: The system must operate reliably in a noisy industrial environment.
Versatility: It should be capable of performing multiple tests, including power consumption, LED luminance, and buzzer functionality, with precise and repeatable results.
System Design and Components
Due to the requirement for fast inspections, the IZAK team designed the inspection system to inspect a batch of four Units Under Test (UUTs) simultaneously. The UUTs are placed inside a fast-loading shelf system that allows for quick and easy loading and removal. Key features of the system include:
1. High-Durability Connectors: Specially designed connectors that can withstand over one million insertions and removals, ensuring long-term reliability.
2. Batch Inspection Capability: The system can inspect up to four UUTs at the same time, significantly increasing inspection throughput.
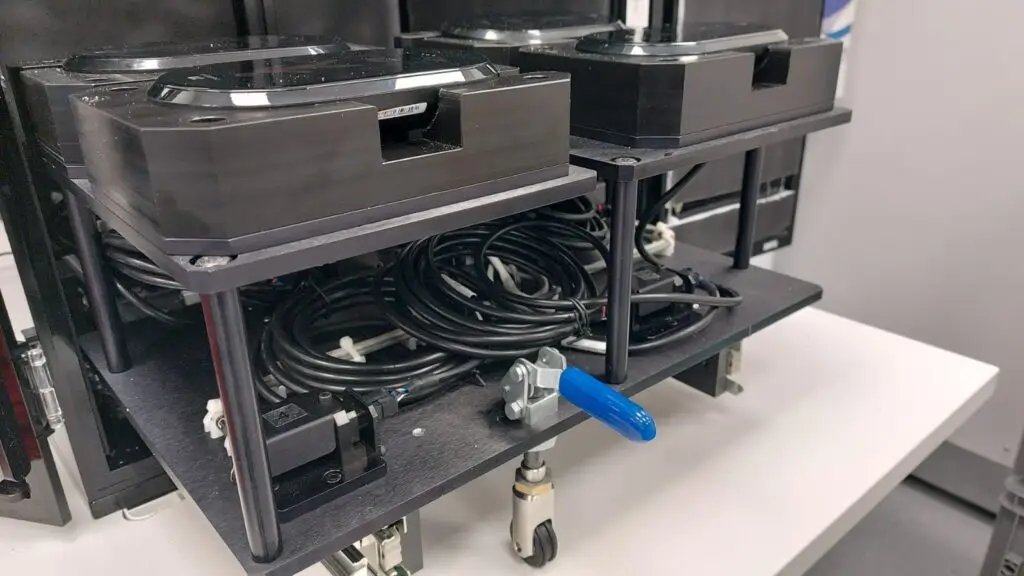
Inspection States:
1. Bare LED Matrix Inspection:
· LED Functionality: Each LED is inspected for proper operation.
· Color and Brightness Levels: LEDs are tested for correct color and brightness.
· Additional Tests: Other performance metrics are also evaluated.
2. Optical Shape Inspection:
· Uniformity and Homogeneity: Checks for uniform illumination across the LED chip surface, ensuring no light leakage and consistent brightness.
· Shape Mask Verification: Captures the LED shape and compares it against predefined templates to verify conformity.
Additional Tests:
- Current and Power Consumption: Ensures that each pin consumes less than the specified current.
- Buzzer Test: Verifies that the on-board buzzer emits sound at specific frequencies when alert signals are activated.
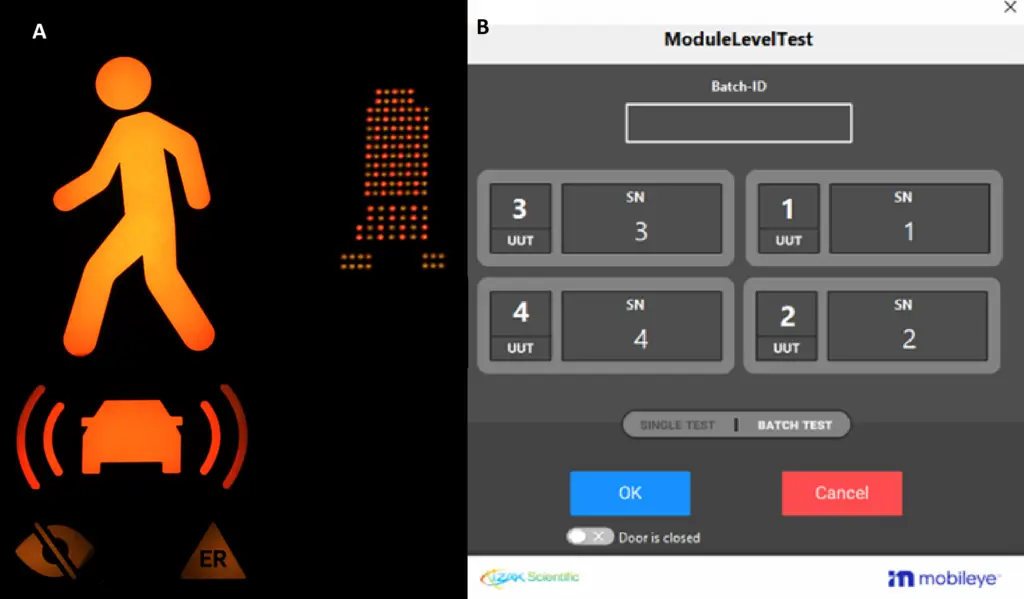
Implementation and Testing
Installation and Setup:
- Initial Setup: The cabinet is secured to a workbench for stability. Shelves are equipped with UUT beds and PCB standoff holders for secure placement of the UUTs.
- Connecting the UUTs: Each UUT is connected to the power supply and designated imaging system through labelled harness connectors.
Testing Procedure:
- Batch Testing: Up to four UUTs are tested simultaneously. The system initiates tests only when all safety interlocks confirm the cabinet doors are closed.
- Automated Process: The testing software developed by IZAK team, automates the entire process, including power supply control, data acquisition from the imaging system, and result logging.
Verification and Validation:
- Power Consumption: Each pin’s current is monitored, and any pin drawing more than the current limit at specific operating voltage results in a fail.
- Luminance and Shape Inspection: The imaging system captures LED outputs and compares them to expected results, ensuring uniform brightness and correct shapes.
- Buzzer Test: The buzzer’s frequency output is measured to ensure it meets the specified frequencies required.
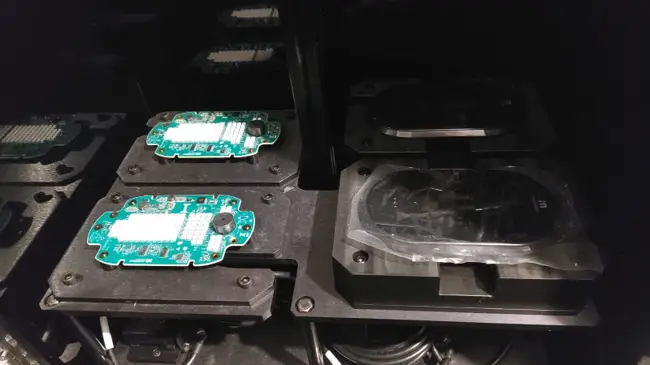
Case Study Results
Our system met all the project requirements, delivering
exceptional performance and reliability. Key outcomes include:
- Durability:
The fast connector demonstrated a lifespan of over 1 million insertions
without failure.
- Speed
and Efficiency: The system consistently performed batch tests in under
30 seconds, maintaining high throughput in the production environment.
- Reliability:
Despite the noisy industrial setting, the system produced accurate and
repeatable results, ensuring high-quality inspections independent of light
background as well as acoustics background.
Conclusion
This case study highlights IZAK Scientific’s expertise in
developing robust, efficient, and high-speed LED inspection systems. Our
solutions are designed to enhance production efficiency, ensure product
quality, and meet the demanding needs of quality assurance and engineering
managers in high-volume production environments.
For more information on how our innovative inspection
systems can benefit your production line, visit IZAK Scientific.
Tzachi Sabati
CEO, IZAK Scientific
Physicist specializing in photonics and quantum technologies, with deep expertise in quantum sensors and advanced optical systems. Leads the Advanced Quantum Lab course at the Technion, bridging academic excellence with industry innovation. At IZAK Scientific, provides cutting-edge photonics-based solutions, developing customized inspection and sensing systems for R&D and production. Passionate about advancing quantum sensing applications and integrating novel technologies to meet industry needs.